01. The Power of Access.
Have you ever pictured in your mind the perfect solution to a problem? The kind of thing where one little piece would have made all the difference, or where a different shape would have turned blocky awkwardness into smooth efficiency? Whether it’s a new creation or a design improvement, many of us have experienced these moments of clarity and wished we could somehow pull it straight from our minds in that moment. Having access to a good workshop is perhaps the next best thing, but few of us have the space, money, or time to accumulate the dozens of tools that a typical shop requires.
There have been ideas for inventions and improvements rattling around in my head for years, but never thought about developing any of them, simply due to that ever-present roadblock: “how?”
Cam St. Louis
02. How it all began.
I’ve spent the past four years developing my own designs for traditional Celtic woodwind instruments such as pennywhistles, flutes, and bagpipes for quite a while, beginning with hand-filing PVC pipe, then borrowing time on a friend’s metal lathe. It quickly became apparent that the bridge between “design” and “execution” was not one I could cross anytime soon with my lousy machining skills and infrequent trips to my friend’s shop.
When I heard about the Facility, and it’s mission of enabling makers to design and prototype almost anything, an idea began to form. On the plane back from Ireland, I started learning to 3D model using a sketch-based design program, and mocked up one of my whistlehead designs. The Facility has a number of additive manufacturing devices, and the sub-millimeter precision of the Form 2 vat-polymerization 3D printer seemed like an ideal way to create what I had envisioned
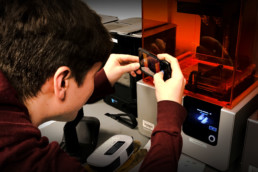
It was pretty thrilling when those first two prototypes rose out of the liquid resin literally dripping with potential. I exercised a lot of patience while they went through the wash and cure cycle.
03. Letting go of limitations.
Back on terra firma, and with the Facility’s brief 2-hour 3D printing class under my belt, I soon watched a much more elegant design slowly rise from the pool of clear goo in the tank. After curing and removing support structures, I was finally able to play an instrument born completely from my own mind without being hindered by the limitations of traditional manufacturing. It played better than anything I had made so far, and I was ecstatic to be able to play an instrument sprung from my own imagination.
Being able to drive development forward this way–printing an incremental series of tests with a highly consistent printer–changed my entire outlook on the project, and beyond that, my mindset in general. The facility has transformed “wouldn’t it be nice…” to “what do I need to know to accomplish this,” and with the Facility I see a way clear forward for each of them, or, failing that, who to ask for help.
Those first parts were only the beginning, but it was clear, even then, that this process was going to open up a lot of opportunities.
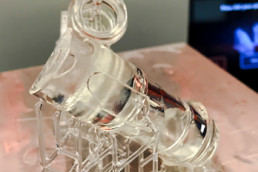
04. Payoff.
Joining such an inclusive community of enthusiastic makers from many different disciplines has been an immense highlight of the last year, and I can’t wait to continue working on this project and others.
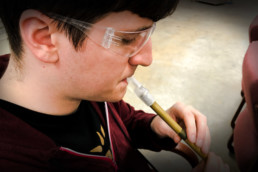